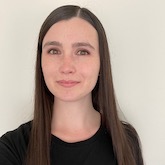
Fulfillment Center Guide for Ecommerce Businesses
by Jaidyn Farar
Fulfillment centers are crucial elements of your supply chain; their design and efficiency influence shipping costs, package security, and delivery time. Whether you take advantage of a 3PL’s fulfillment centers or run your own facilities, it’s important to understand how these buildings work.
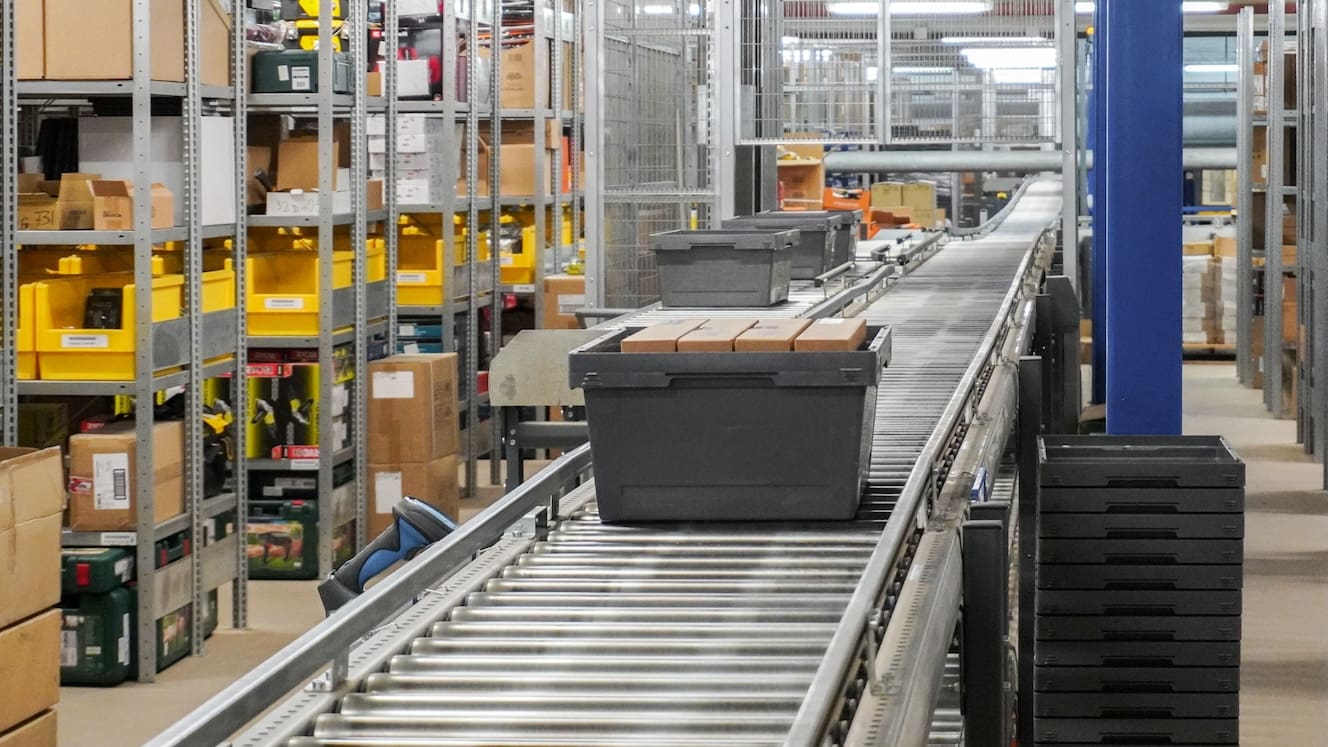
What is a fulfillment center? What does a fulfillment center do? In this article, we’ll answer both of these questions and give you some tips to improve your order fulfillment process.
What is a fulfillment center?
A fulfillment center is a logistics facility used to handle order fulfillment tasks such as inventory storage, picking, packing, and shipping—all the processes used to send something from a seller to an end customer.
The goal of every fulfillment center is to deliver orders to customers on time while keeping labor, material, and transportation costs as low as possible.
Businesses sometimes work with third-party logistics providers (3PLs) to outsource their order fulfillment. They store their inventory in the 3PL’s fulfillment centers, and 3PL staff members handle order fulfillment processes.
While the terms warehouse and fulfillment center are often used interchangeably, it’s worth knowing the subtle differences between them.
Fulfillment center vs. warehouse
Is a fulfillment center the same as a warehouse? Not quite. While fulfillment centers are used to store inventory for short periods before shipping it out, warehouses are usually used for long-term inventory storage.
Fulfillment centers are most useful for B2C (business-to-consumer) businesses, or those that ship directly to consumers. Warehouses are often used for B2B (business-to-business) fulfillment, which generally deals with large wholesale orders.
Warehouses and fulfillment centers differ in the following ways:
- Storage time. The goal of a fulfillment center is to keep inventory flowing, so goods are quickly shipped to customers and replaced by incoming stock. Ideally, inventory shouldn’t stay in a fulfillment center for more than a month. On the other hand, the goal of a warehouse is usually to store items for long periods.
- Operations. Operations at a fulfillment center look very different from those at a warehouse. Fulfillment centers are hubs of activity, where employees and technology collaborate to receive inventory, pick and pack orders, and ship out hundreds or thousands of packages a day. In contrast, warehouse activities include receiving, storage, and occasionally shipping large orders.
- Carrier pickup frequency. Because fulfillment centers usually serve ecommerce businesses, they have frequent carrier pickups—often multiple per day, depending on cutoff times for next-day and overnight shipments. Warehouses can get by with fewer carrier pickups, which saves money.
Fulfillment center vs. distribution center
Fulfillment centers and distribution centers (DCs) are both facilities that receive inventory and store it for short periods. However, fulfillment centers are designed to ship products to individual consumers, while distribution centers are most commonly used to distribute inventory to retailers or fulfillment centers.
How a fulfillment center works
Sellers use fulfillment centers to store inventory short-term and prepare customer orders for shipping. Once an online order is placed, the information is passed to the proper warehouse systems. Workers pick and pack products, add shipping labels, and send them off with carriers at scheduled pickup times.
Some businesses don’t own or operate their own fulfillment centers, instead partnering with one or more 3PLs. Others, preferring to retain hands-on control of their logistics operations, invest in the facilities, technology, and labor required to handle fulfillment in-house.
The following activities all take place in fulfillment centers:
Receiving
Receiving involves accepting and unloading incoming inventory shipments, inspecting items for accuracy and damage, and logging them into the inventory management system. Automation tools like barcode scanners and RFID technology speed up this process, reduce human error, and improve efficiency.
Storage
Products are assigned to designated areas of a fulfillment center, where they’re stored using shelves, racks, or bins. Large, complex facilities often use technology like automated storage and retrieval systems (AS/RS) to maximize storage space and accessibility. Businesses also use warehouse management systems (WMS) to keep track of inventory locations, which helps pickers find the right products when it’s time to retrieve them.
Inventory management
Inventory management involves tracking stock levels and reordering inventory when it gets low. The goal of inventory management is to have exactly the right stock levels to meet customer demand, avoiding costly stockouts and overstocks. Inventory management software automates the reordering process and provides visibility into stock levels and movement.
Order processing
When a customer makes an online purchase, their order information is transferred from the ecommerce platform to an order management system (OMS), where the details are verified. Then the system generates a pick list that shows workers where to find the product(s) in the order.
Picking and packing
Picking is the process of retrieving items from storage, while packing is the process of preparing them for shipment. Fulfillment center staff, often aided by automated systems like pick-to-light or voice picking technology, locate the correct items. They then send the products to packing stations, where other workers put them in boxes and prepare them for shipping.
Because picking and packing are some of the most time-consuming fulfillment processes, organizations are constantly on the lookout for ways to streamline and automate these tasks.
Kitting
Kitting involves assembling individual items into ready-to-ship kits or bundles based on customer orders. Bundling products together increases packing efficiency and can lower shipping costs. Kitting is often used to fulfill subscription orders.
Shipping
Once orders are picked and packed, they’re handed over to shipping carriers. Carriers transport packages from one carrier facility to another before delivering them to end customers. Although carriers have hands-on control over the last-mile delivery process, businesses can (and should) monitor shipping metrics and work with carriers to resolve issues like frequent delays or package loss.
Returns management
Fulfillment centers don’t just send packages out—they’re also used to receive inbound packages that have been returned. Returns management involves receiving, inspecting, and processing returned items from customers. Once these goods have been inspected, fulfillment center workers decide whether to dispose of them, restock them, or refurbish them.
Fulfillment centers and shipping carrier relationships
When thinking about fulfillment centers, it’s easy to only consider the work that happens inside the four walls: receiving inventory, storing it, and later picking products and packing boxes. But what about shipping?
Fulfillment centers constantly send out packages with carriers, who deliver them to consumers. Because of the essential role carriers play in order fulfillment, you need to carefully select the best carriers for your shipping needs and develop strong partnerships with them. Negotiating rates by shipping volume will save money, allowing you to pass down cost savings to your customers by offering more affordable shipping options.
To build strong carrier partnerships and get the best deals on shipping, we recommend using a solution like EasyPost Enterprise to automatically integrate with multiple carriers, optimize for delivery cost and speed, and access features like tracking and address verification.
Should you automate your fulfillment centers?
Many organizations add automation technology, including both software and robotics, to their fulfillment centers to improve efficiency, employee safety, and sustainability.
Automating your fulfillment centers streamlines inventory handling and order processing, drastically reducing the time and labor required for these tasks. This efficiency translates to lower operational costs and faster order fulfillment, ultimately leading to greater customer satisfaction.
Contrary to popular belief, automation doesn’t force human workers out of jobs. Instead, technology is used to handle repetitive, strenuous tasks that employees generally don’t want. This opens up opportunities for people to oversee more interesting fulfillment center processes.
Automated systems also lead to more accurate inventory management and optimized space utilization. This reduces waste and energy consumption, contributing to more sustainable operations.
Many people think automation refers only to robotics, but automation technology also includes software. When you use an OMS, WMS, inventory management system, shipping software, and other systems to run your fulfillment centers more efficiently, you’re taking advantage of automation. Not only do you optimize processes, but you also eliminate human errors that could potentially cause bottlenecks and delays.
Choosing a 3PL fulfillment center
Thinking of outsourcing fulfillment to a 3PL? Let’s review when to consider working with a 3PL, some potential benefits, and factors to consider when choosing a partner.
When to partner with a 3PL fulfillment center
If you lack supply chain expertise, outsourcing fulfillment can help expand your market reach and improve delivery times. Consider partnering with a 3PL when order volumes exceed the capacity of your in-house logistics operations.
Benefits of using a 3PL fulfillment center
For fast-growing, mid-sized to enterprise-level businesses, outsourcing fulfillment comes with several advantages.
- Reduced costs. Third-party logistics providers offer economies of scale, allowing their partners to benefit from reduced shipping rates and more efficient use of warehouse space. The result? Cost savings in both shipping and storage.
- Streamlined order fulfillment. Outsourcing order fulfillment allows businesses to speed up the picking, packing, and shipping processes, ensuring faster delivery times.
- More time to focus on the big picture. Partnering with a 3PL gives you more time to concentrate on strategic growth initiatives, such as product development and market expansion.
- Access to logistics expertise. A 3PL brings specialized knowledge and experience in logistics, helping businesses navigate complexities in supply chain management.
Of course, working with a 3PL isn’t for every organization. Potential downsides include reduced control over the fulfillment process, communication challenges, and the risk of dependency on an external provider. Consider your business needs, goals, and growth rate when deciding whether to outsource order fulfillment.
Factors to consider when choosing a partner
When evaluating 3PLs, consider the following factors to determine which partner is right for your business.
- Scalability. Can the 3PL handle your shipping volume as your business expands?
- Technology. Does the 3PL provide access to advanced logistics technologies that integrate with your systems?
- Accuracy. How accurate are the 3PL’s inventory management and order fulfillment processes?
- Value-added services. Does the 3PL offer value-added services such as custom packaging, kitting, and assembly?
- Customer service. Does the 3PL provide robust customer service, including dedicated support teams and responsive communication?
- Pricing. Does the 3PL’s pricing model align with your budget?
What about Amazon fulfillment centers?
Businesses that sell on Amazon sometimes use Fulfillment by Amazon (FBA) to fulfill their orders. With FBA, you ship your inventory to Amazon’s fulfillment centers, where it’s stored until customers make purchases. Like any other 3PL, FBA charges storage fees that can cut into the profit margins of smaller sellers. In addition, using FBA can increase your number of returns because of Amazon’s generous returns policy.
Fulfillment center technology that saves time and money
Keeping order fulfillment in-house allows you to maintain full control over every process. You can ensure that products are high-quality and work directly with carriers for a great last-mile delivery experience, one that boosts customer satisfaction.
An important part of your fulfillment process is using the right technology. And when it comes to shipping, it’s especially important to have a solution that scales with your business. EasyPost Enterprise Shipping is a system for high-performance shippers. With on-premise and cloud options available, EasyPost Enterprise gives you the flexibility to handle your order volume even during your busiest times of the year.
Get in touch with us to unlock more streamlined shipping with EasyPost Enterprise.